压力管道年度检测
压力管道是指利用一定的压力用于输送气体或者液体的管状设备。压力管道在长期的高压运行过程中,可能会因腐蚀、磨损或疲劳等因素导致材料性能逐渐下降。定期检测可以及时发现潜在的安全隐患,采取有效措施预防事故的发生,同时优化管道的运行和维护策略,减少因故障停机带来的经济损失,提高生产效率。
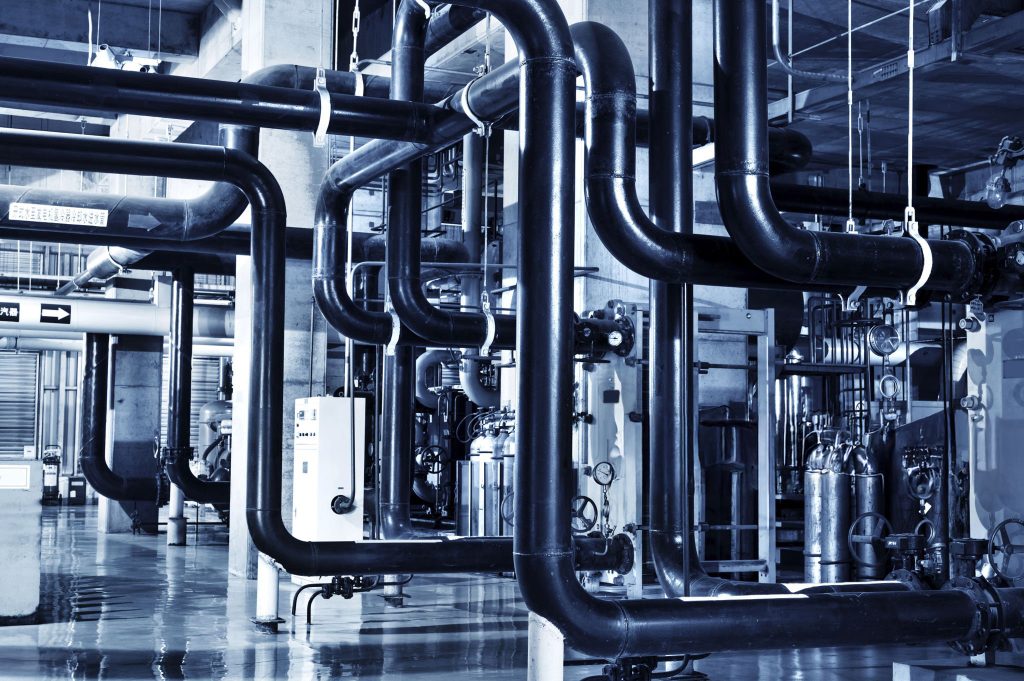
检测内容:
1.视觉检查:通过肉眼或借助放大镜、内窥镜等工具检查管道的外部和内部状况,如腐蚀、裂纹、变形等。
2.无损检测:使用超声波检测、射线检测、磁粉检测和渗透检测等技术,探测管道内部的缺陷。
3.压力测试:对管道进行压力测试,验证其承受预定压力的能力,确保管道的强度和完整性。
4.泄漏检测:使用气体泄漏检测器、热成像相机等设备检测管道的泄漏情况。
5.腐蚀监测:通过定期取样分析或在线监测系统评估管道材料的腐蚀状况。
6.壁厚测量:使用超声波测厚仪等工具测量管道壁厚,评估腐蚀或磨损对管道壁厚的影响。
7.材料分析:对管道材料进行化学和物理性能分析,确保材料符合设计和安全要求。
8.振动分析:监测管道的振动情况,识别可能导致疲劳破坏的异常振动。
9.年度检查:包括管道安全管理情况、管道运行状况和安全附件与仪表的检查,必要时进行壁厚测定和电阻值测量。
10.完整性管理:结合上述检测结果,进行管道完整性评估和管理,制定维护和修复计划。
检测方法:
检测方法 | 原理 |
射线检测(RT) | 射线在穿透物体过程中会与物体发生相互作用,因吸收和散射而使其强度减弱。强度衰减取决于物质的衰减系数和射线在物质中穿越的厚度。如果被透照试件的局部存在缺陷,而构成缺陷的物质衰减系数有不同于试件,该局部区域的透过射线强度就会与周围产生差异。底片上相应的部位就会出现黑度差异,评片人员据此判断缺陷情况。 |
渗透检测(PT) | 渗透检测是一种以毛细作用原理为基础,检查表面开口缺陷的无损检测方法。渗透检测可以用于金属及非金属工件的表面开口缺陷检测,不受被检工件的结构、化学成分以及缺陷形状的影响。但是常规渗透检测无法或难以检查多孔的材料,也不适用于检测因外来因素造成开口被堵塞的缺陷。 |
目视检测(VT) | 目视检测主要依赖于人眼对物体外观、形状、颜色、纹理等特征的敏感性和判断力,结合光线、角度等条件,发现并记录表面的缺陷、裂纹、疵点等问题。 |
超声检测(UT) | 超声检测是利用超声波在材料中传播时,遇到不同声阻抗界面会产生反射和折射的原理,通过分析反射回来的超声波信号来评估材料的内部结构和可能存在的缺陷。 |
磁粉检测(MT) | 铁磁性材料工件被磁化后,由于不连续性的存在,使工件表面和近表面的磁力线发生局部畸变 而产生漏磁场,吸附施加在工件表面的磁粉,在合适的光照下形成目视可见的磁痕,从而显示出不连续性的位置、大小、形状和严重程度。 |
衍射时差检测(TOFD) | TOFD技术采用一发一收两个宽带窄脉冲探头进行检测,探头相对于焊缝中心线对称布置。发射探头产生非聚焦纵波波束以一定角度入射到被检工件中,其中部分波束沿近表面传播被接收探头接收,部分波束经底面反射后被探头接收。接收探头通过接收缺陷尖端的衍射信号及其时差来确定缺陷的位置和自身高度。 |
相控阵检测(PAUT) | 相控阵超声检测的基本概念来源于相控阵雷达技术,最早仅用于医疗领域。探头由若干个独立的压电晶片按一定的规律分布排列,通过软件可以单独控制每个晶片的激发时间,从而控制发射超声波束的形状和方向,实现超声波的波束扫描、偏转和聚焦。 |
压力管道分类:
工业管道、动力管道、蒸汽管道、空压管道、输油管道、长输管道、公用管道、输气管道、燃气管道、热力管道、压力金属管道等。
检测周期:
1.在线检验:在线检验是在压力管道运行条件下进行的检验,通常每年至少进行一次。
2.全面检验:全面检验是更详细的检验,需要暂停管道的运行。检验周期根据压力管道的安全状况等级而定:
- 安全状况等级为1级和2级的压力管道:全面检验周期一般不超过6年。
- 安全状况等级为3级的压力管道:全面检验周期一般不超过3年。
- 特殊情况:在某些特殊情况下,如发现严重腐蚀、承受交变载荷、材质劣化或日常体检中发现严重问题等,检验周期可能需要缩短。
- 这些检验周期的规定旨在确保压力管道的安全运行,及时发现和处理潜在的安全隐患,从而保障生产安全和环境保护。
服务流程
Service Process
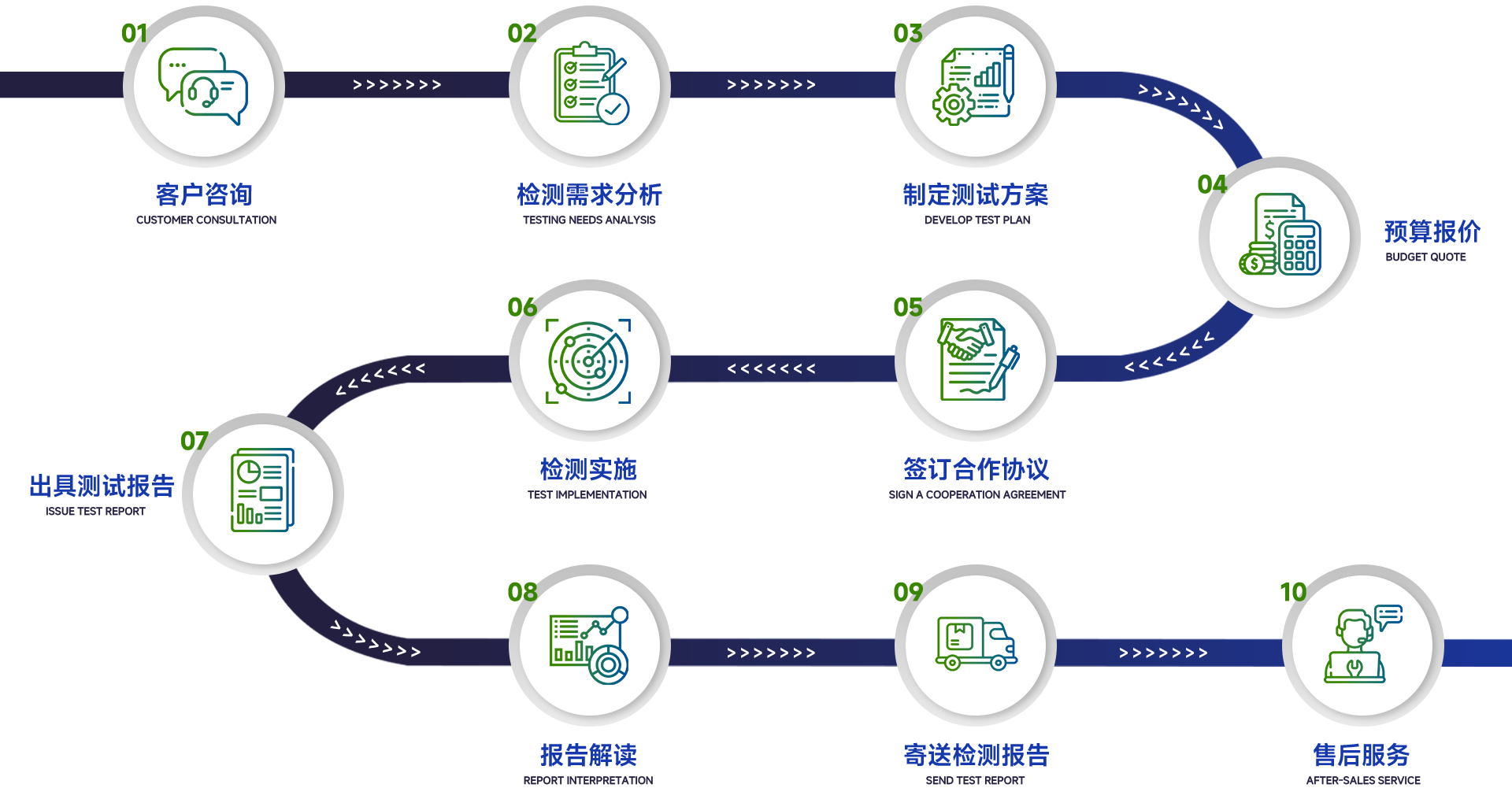
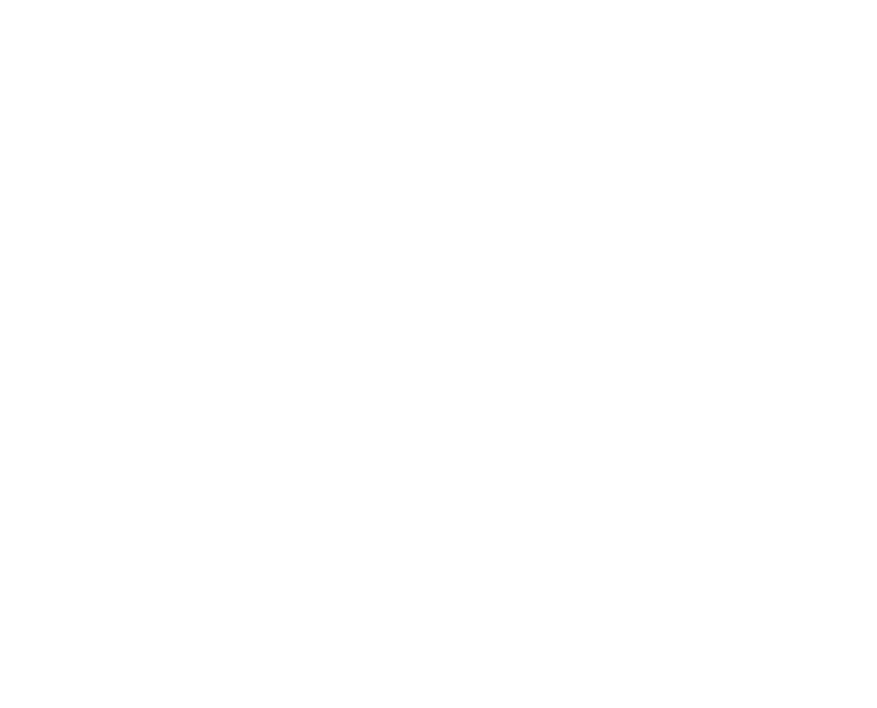
热线电话
联系我们
- 办公试验地址:广东省深圳市龙岗区龙岗街道五联社区规划路 5-1 号 101
- 行政办公地址:深圳市龙岗区龙城街道龙平西路仁恒梦创广场 B 塔办公楼第 19 层 03 单元
- 检测咨询:18623283720 / 13392822312
- 电话:0755-83139629
- 邮箱:Huayi9629@163.com
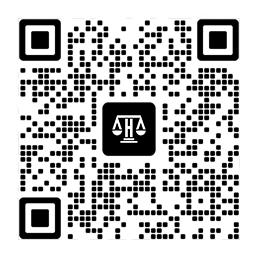
业务咨询
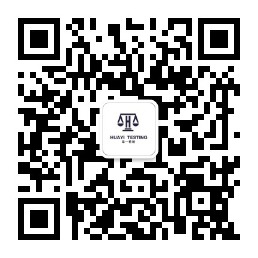
关注微信公众号
法律声明 | 友情链接
Copyright © 2024深圳华一检验有限公司. All Rights Reserved. | 粤ICP备**********号-1